Project
Cutting down water consumption in the pharmaceutical industry
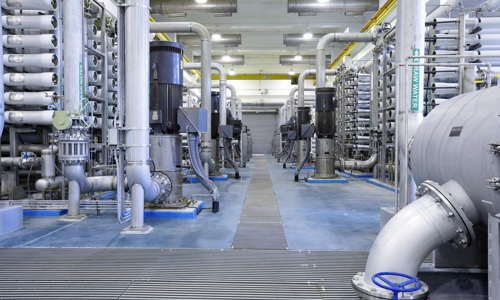
Credit: TerryJ
Project
Credit: TerryJ
Reducing and reusing water consumption is becoming an increasingly important part of pharmaceutical manufacturers’ strategic sustainability plans. The pharmaceutical industry is water-intensive and production processes are designed to be resilient and ensure patient safety and thus require extensive cleaning processes. Adding to that, restrictions on water consumption due to among other things, legislation and drought, are becoming even tighter, which is prompting companies to rethink their water management.
And rethinking is key when it comes to the production water. There are significant reductions to be made in all steps of the production process, one of them being CIP.
NIRAS has been working with a large-scale pharmaceutical company to mitigate their water issues, investigating the CIP process to make it more water-efficient. A CIP is designed to clean used equipment with copious amounts of water (up to 45% of the total water consumption at the site). Currently, this wastewater is sent to the wastewater treatment plant for treatment. In the case of the pharmaceutical manufacturer, NIRAS’s solution was to clean spent CIP water and reuse it back into production.
In this effort, there are significant challenges to removing the impurities in the water. There can be a wide range of chemical and biologicals in the water, and since the product produced is unknown, the purification process needs to be designed to handle the worst-case scenario . In this effort, there were six potential streams of interest; purified water (WPU) used as pre-rinse, caustic wash, rinse with WPU, acid wash, rinse with WPU, and a final rinse with water for injection (WFI). Out of the six potential streams, four of the streams used copious amounts of water to clean out a tank and pipes.
An in-depth water analysis was done on the process to have a better understanding of what was going on. This analysis included testing for bioburden, organic pollutants, nitrogen, phosphorous, heavy metals, oils, etc. just to design a correct treatment train and meet any standard imposed by the facility and the legislative agencies. Then, using a risk assessment in conjunction, the correct treatment setup would be identified.
In the end, some of the streams will be treated and used again within the process. Some other streams will be treated with reverse osmosis membranes and re-used with the drinking water entering the facility . These membranes can separate impurities from water and produce clean water which after validation should be higher than the drinking water coming into the facility. This will lead to a 19% reduction of water at the site. While the project is ongoing and there are a lot of steps needed to be completed, 19% in water reduction is a lofty goal. In another project, discharged water from utility systems is collected and cleansed in RO to remove salt sand likewise before being mixed with the drinking water used for production purposes. Combining these two water-saving initiatives, up to a 44% reduction in water consumed on site can be achieved.
The team at NIRAS thoroughly analyzed and identified the correct water streams to select the correct technology to clean this water. The end goal is to reuse the water back into production and ensure the water complies with drinking water standards and pharmaceutical guidelines for WPU, respectively.