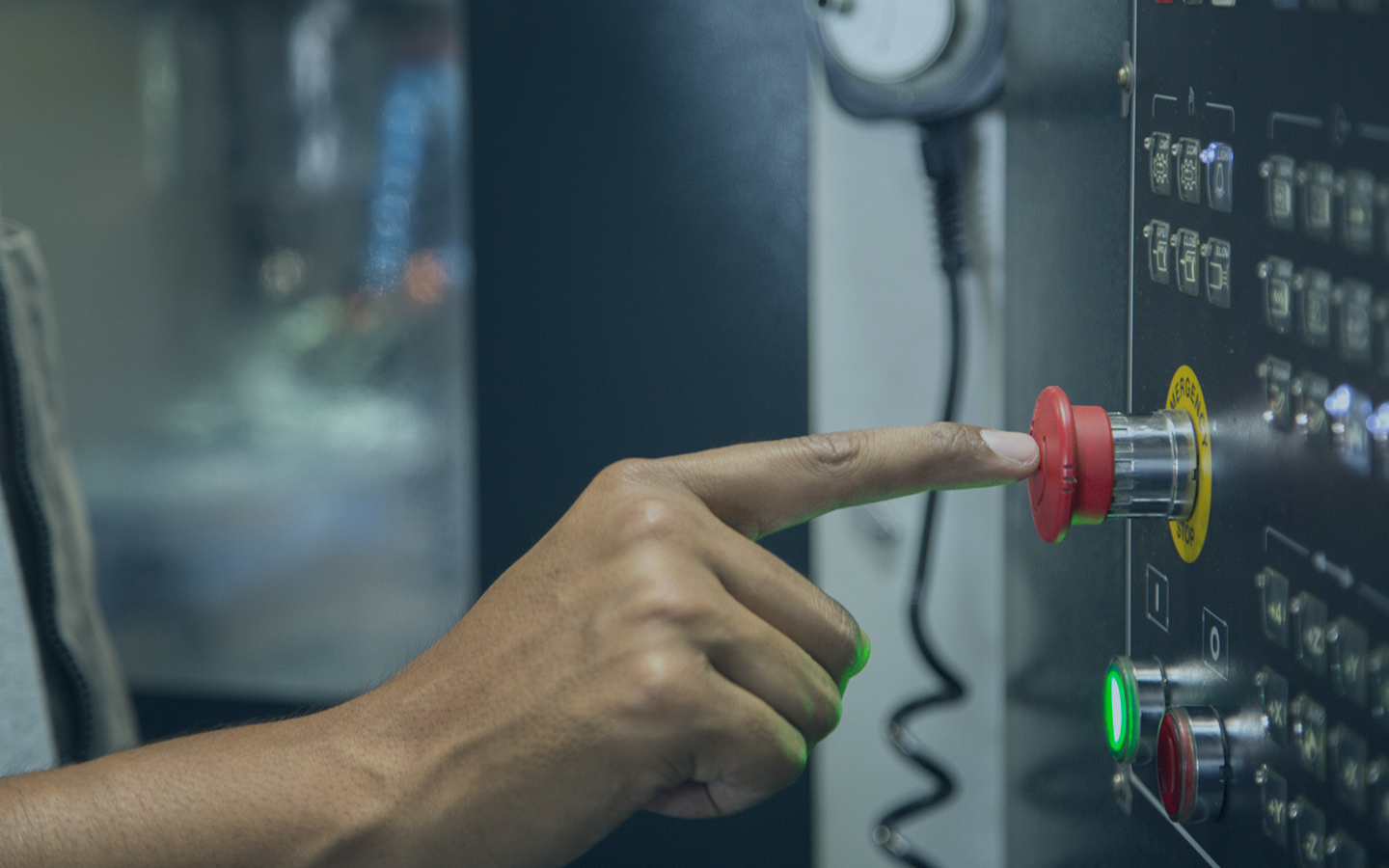
Safety Compliance
Our certified Functional Safety Engineers (FS Eng) work with global and large-scale food, beverage, and pharmaceutical manufacturers to ensure start to end safety validation of the complete production line, evaluating against harmonized EU standards and handling everything from machine safety validation to ATEX certification management.
Navigate the Complexity of Safety Compliance with NIRAS
Maintaining safety in increasingly complex industrial environments is a significant challenge. Ensuring safety compliance can be both intricate and costly, demanding substantial up-to-date knowledge and resources. NIRAS offers cost effective, comprehensive safety compliance services, providing the engineering expertise you need to maintain a safe working environment, improve operational efficiency and reduce downtime.
Our Compliance Services
Our wide range of services designed to meet your safety compliance needs include:
- Machine Safety Assessment and Reporting (PUWER, AUWED)
- Safety Validation of Control Systems
- CE Marking for Complex Assemblies
- ATEX Certification and Assessments
- Explosive Atmosphere Basis of Safety (DSEAR, ATEX, NFPA)
- Hazardous Area Classification (HAC)
- Process Safety (HAZOP, FMEA, Safety & Operability Review)
Industry Expertise
We serve a diverse range of industries with extensive experience, including but not exclusive to:
Food, beverage, and brewing
- Snack foods forming and packing
- Dairy and beverage filling/packing
- Sugar processing and packaging
- Bottling and canning lines in breweries
- Meat butchering and preparation
- Ready meals, pies, and pastries
Life Sciences
- Pharmaceutical manufacturing
- Surgical implant & Medical devices
- Speciality & fine chemicals manufacturing
- Biotechnology and bioprocessing
- Health and beauty products manufacturing
- Inks, dyes and coatings
Why Choose NIRAS for all your compliance needs?
Expertise and experience
Our specialist Compliance team at NIRAS consists exclusively of highly qualified engineers. This includes certified Functional Safety Engineers (FS-Eng), HAZOP leads, CompEx professionals, and Certified Machine Safety Engineers (CMSE). With a large team of specialists, we can manage extensive projects over multiple client sites efficiently, offering reliability, and economies of scale. Our technical prowess and project management expertise ensures that we can tackle complex safety challenges with confidence and precision.
Comprehensive, versatile solutions
NIRAS offers end-to-end compliance services, covering all safety and regulatory needs. From machine safety assessments to process safety, we provide comprehensive solutions that focus on HAZOPs and ATEX Directives. Our versatile approach ensures that we can address a wide range of safety concerns, providing tailored solutions to meet the specific needs of our clients.
Safety and compliance
At NIRAS, we pride ourselves on our regulatory expertise. We ensure that our clients meet all regulatory requirements efficiently. Our full spectrum of services includes feasibility assessments, safety courses, and ATEX training. By partnering with us, you can be confident that your operations will comply with the latest safety standards and regulations.
Innovation and technology
We leverage the latest technologies and best practices to conduct thorough HAZOPs and ATEX assessments. Our commitment to staying at the forefront of industry advancements means that we continuously improve our methodologies and tools, ensuring the highest level of safety and efficiency for our clients.
Client success stories
NIRAS has a proven track record of success, demonstrated by our work with global clients.
Addressing HAZOP implementation challenges
Implementing HAZOP studies can be challenging due to their time-consuming and resource-intensive nature, especially for complex processes. Our multidisciplinary team, with its vast experience and international reach, overcomes these challenges, ensuring the effectiveness and quality of each study. The success of a HAZOP study heavily relies on the knowledge and skills of the team members and the thoroughness of the documentation and analysis. At NIRAS, we excel in delivering high-quality outcomes, making your investment in HAZOP studies worthwhile.
HAZOP services
A Hazard and Operability Study (HAZOP) is a structured technique widely adopted in high-risk industries such as chemical, pharmaceutical, and oil and gas, to identify and evaluate potential risks before they occur to personnel, equipment, and the environment, ensuring safe operation.
Businesses have a moral, legal and business requirement to identify hazards, and over the past few decades, the HAZOP studies has proven to be a powerful tool for identifying process hazards. A well-executed HAZOP study therefore provides a good basis for project stakeholders to demonstrate that they have provided a sound basis of due diligence over the design.
NIRAS provides comprehensive Hazard and Operability Studies (HAZOP) to help meet these critical obligations. Our expertise ensures that your processes adhere to the highest safety standards, mitigating risks and enhancing operational efficiency.
We maintain detailed documentation of our HAZOP studies to demonstrate compliance with Good Manufacturing Practices (GMP) and Good Laboratory Practices (GLP). This includes conducting thorough risk assessments, developing mitigation plans, and validating control measures. Regular reviews and audits are also part of our services, ensuring that HAZOP assessments are updated to reflect changes in processes, equipment, or regulations. These audits often include detailed reviews of HAZOP documentation to ensure ongoing compliance.
The HAZOP process
HAZOP studies are conducted by a multidisciplinary team, including process engineers, control engineers, safety professionals, and operators. Using specific guide words, the team systematically explores potential deviations from normal operations. Common guide words include "No," "More," "Less," "As well as," "Part of," "Reverse," and "Other than." The process is divided into sections or "nodes," usually corresponding to specific equipment or control points. The team identifies how each guide word could apply to various parameters such as flow, temperature, pressure, and composition to identify deviations from the design intent. Possible causes and potential consequences for each identified deviation are discussed, considering existing safeguards and their adequacy. The team then recommends actions to mitigate or eliminate identified risks, which may include design changes, additional safety measures, procedural changes, or further analysis.
Benefits of HAZOP
HAZOP studies offer numerous benefits. They provide systematic identification of hazards, which improves safety by addressing potential safety issues before they occur. They help meet regulatory requirements and industry standards for process safety. Additionally, HAZOP studies enhance operability and reliability by identifying potential operational issues that could impact production.
When to conduct a HAZOP
HAZOP studies should ideally be conducted during the design phase of a new process or modification to identify and mitigate risks early. They are also used for existing processes to review and improve safety and operability. Following an incident, HAZOP studies are conducted to understand and address potential hazards that were not previously identified.
For example, consider a reactor node with the parameter of temperature. Using the guide word "More," the deviation might be a temperature higher than intended. Possible causes could include a faulty temperature sensor, control system failure, or an exothermic reaction out of control. Consequences might involve overpressure, rupture, or the release of hazardous materials. Existing safeguards might include temperature alarms, pressure relief valves, and an automatic shutdown system. Recommendations could include improving sensor reliability, installing redundant sensors, and enhancing operator training on response procedures.
ATEX compliance services
Ensuring safety and regulatory compliance in explosive atmospheres is a critical concern for many industries. NIRAS offers comprehensive ATEX services to help you navigate this complex landscape. "ATEX" stands for "Atmosphères Explosibles," referring to two European Union directives aimed at regulating environments with risks of explosions due to flammable gases, vapours, mists, or combustible dusts.
Understanding ATEX Directives
The ATEX framework includes two key directives:
ATEX 95 (Directive 2014/34/EU) focuses on regulating equipment and protective systems intended for use in potentially explosive atmospheres. This directive applies to all electrical and mechanical devices, control systems, and safety equipment used in such environments. To ensure safe operation, equipment must be designed, tested, and certified by a Notified Body, and must carry both the CE marking and the specific ATEX marking.
ATEX 137 (Directive 1999/92/EC) centres on the health and safety of workers who may be at risk from explosive atmospheres. This directive mandates that employers assess explosion risks, classify hazardous areas, and implement protective measures. Employers are required to conduct risk assessments, provide appropriate training, and ensure all equipment used in hazardous areas meets stringent safety standards.
Benefits of ATEX compliance
Adhering to ATEX directives enhances the safety of both equipment and workers in hazardous environments. It ensures regulatory compliance, helping to avoid legal and financial penalties. Furthermore, meeting ATEX requirements allows manufacturers to sell equipment within the EU, broadening market access.
Why choose NIRAS for all your compliance needs?
NIRAS offers expert ATEX compliance services to guide you through the complexities of these directives. Our team ensures that your equipment and processes meet all safety standards, providing you with peace of mind and ensuring regulatory compliance. By choosing NIRAS, you can effectively mitigate the risks associated with explosive atmospheres, ensuring the safety of your operations and the well-being of your workers. Learn how we can support your safety compliance needs by contacting one of our experts.
Reach out
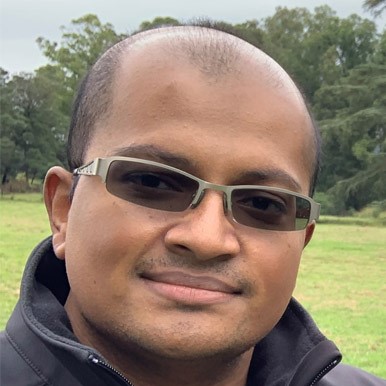
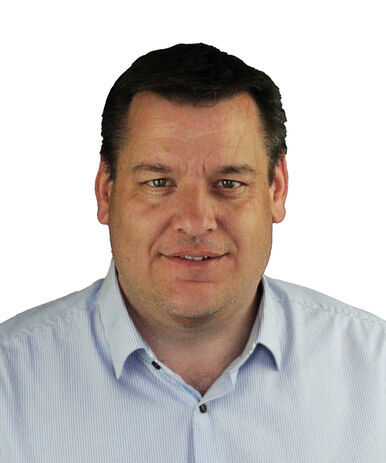