Project
Reliability and flexibility come together at Royal FrieslandCampina in the Netherlands
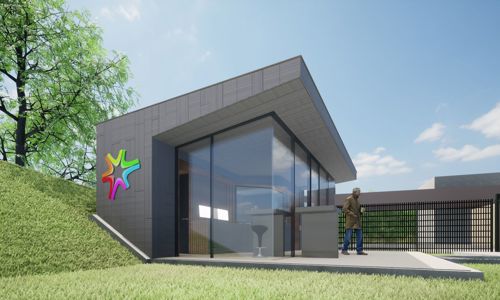
Project
Royal FrieslandCampina has various production facilities in the Netherlands. The one in Lochem is particularly interesting.
The site is interesting because it houses three different factories where milk is processed into butter, milk powder, and specific ingredients. Each production day is different because in addition to running continuous production, the location also serves as a backup if production at other sites should fail. The Lochem site is a dynamic environment in which NIRAS contributes to various projects that promote reliability, flexibility, and safety.
Renewal and innovation
The production site has a rich history dating back to 1906. The factories have hardly ever stood still due to their significant role, and the original foundation structure is still there in some places despite the changes and innovations that have been implemented over time. Xander ten Hove, Portfolio Manager CAPEX projects, and Oswin Verkerk, Project Manager CAPEX projects at FrieslandCampina, have seen this method used at other projects as well - because production stops are not easily scheduled, but keeping the buildings, grounds, production lines, and other aspects, up-to-date is crucial for the future.
‘Renewal and innovation provide the flexibility we need to adapt within the larger Royal FrieslandCampina organisation.’
Xander ten Hove
In addition to renewal and replacement, there is a strong focus on innovation. The strategic choices made by the global organisation are reflected in the projects at FrieslandCampina Lochem. At Lochem, you quickly notice that in every project, the scopes are interconnected and must be seen within the broader context, both on-site and within the FrieslandCampina network. Implementing an innovative solution in one area leads to renewal or replacement in another, which, in turn, generates a subsequent focus point, and so on. This is where NIRAS Nederland's contributions to e.g. maintaining oversight, leveraging technical expertise, and fostering a stable partnership, prove valuable.
A growing partnership
Due to a need for various building-related elements, Ruud Koetsier, Senior Project Manager, became involved in various projects. And because of the projects’ tendency to grow larger and more complex, Ruud eventually advised involving other NIRAS colleagues. This included not only those in the Building department but also other disciplines such as process engineering, technology, and packaging engineering.
The current project portfolio in Lochem is difficult to manage solely by the in-house project engineering department and benefits from a broad range of knowledge and additional resources. Thanks to NIRAS’s experience and the support from Building, as well as from the other disciplines, adjustments can be made swiftly, and missing team roles can be filled.
Xander and Oswin also note that the collaboration is solid. Everyone appears to be direct colleagues who take responsibility, are involved, and trust each other. According to both parties, this is partly due to the way that FrieslandCampina Lochem employees involve Ruud and his colleagues in related company events.
Another factor is the development of a core team which is always available. You have designated contact persons who coordinate with each other, share knowledge as needed, and potentially involve other NIRAS colleagues if the need arises. This not only includes the Netherlands but also leverages the knowledge of NIRAS branches elsewhere. All of this ensures clarity and efficient use of valuable time, with minimal to no handover required.
‘NIRAS and this production site are now so well-coordinated, even in terms of project approach, that we can delegate a portion of our projects.’
Xander ten Hove
An aligned project approach
The approach of NIRAS Nederland largely aligns with that of FrieslandCampina. Both aim to maintain an overview in each phase, considering choices, budget, schedule, involved parties, and resources. Being realistic and transparent, expressing expectations, and monitoring objectives and conditions allow for adjustments, reducing the chances of surprises. It can happen that the planned budget is unrealistic or that elements of a schedule overlap or need expansion, but by monitoring these aspects within the project at each step, results can be achieved. A big plus since a high degree of predictability is crucial for Royal FrieslandCampina.
A good example is the fire safety project. Improving fire safety across the entire site involved a series of subprojects. Each section of the production site was examined for improvements, scheduling, budget, stakeholders, permits, and other elements. For all these different parts, an overarching communication structure was established among the property owners. Despite being subprojects, everything was somewhat interconnected. Thorough preparations and coordination, along with adjustments to work activities as needed, ensured minimal disruption from the significant improvements made.
Another notable example is managing the wastewater flow on-site. By looking at the route differently, a portion of the wastewater could be, not only better controlled, but also discharged without corrective measures. NIRAS contributed solutions, including project management and engineering.
‘The old situation is almost unimaginable. Fortunately, there have been no major traffic incidents, but the site is now much more organized and, as a result, safer. Despite the large number of logistical movements, the site exudes a sense of calm.’
Oswin Verkerk
One more great example is securing the production site from the outside world. Previously, there was a public road running between various buildings. To make the site safer, more organized, and compliant with regulations, a fence and a new security checkpoint were established in collaboration with NIRAS. It was a project involving many stakeholders where maintaining oversight was crucial.
For fire safety, hygiene, and (traffic) safety, increasing the site's reliability is paramount. Preventing emergencies ensures stability and room to handle excess production from other factories and invest further in innovation.
FrieslandCampina Lochem is strong, yet never motionless. This is evident from the recent activities and future plans. Sustainability is a goal deeply embedded in projects. It is integrated into everything they do and, according to Xander and Oswin, can be emphasized even further. Nevertheless, safety, reliability, and flexibility remain the top priorities as they underpin the existence of this dynamic production site.