Project
Maple Leaf Foods: One of the world's most technologically advanced poultry-processing plants
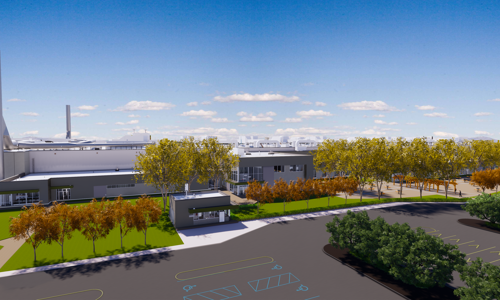
Project
Maple Leaf Foods involved NIRAS in the overall planning of its new 660 mill CAD$ state of the art poultry processing plant in Ontario. NIRAS facilitated the master planning and design to tender phase as subject matter expert and project facilitator.
Maple Leaf Foods is making the largest single investment in the history of the Canadian food industry in order to carry out a strategic overhaul of its poultry production facilities. The overhaul will align current and future production structure with a growing market.
The state-of-the-art poultry plant will merge three existing plants into a brand new production facility with a capacity of 75 to 100 million birds a year. Overall plant capacity will be 2 x 13,500 birds per hour (bph) with an option to increase to 2 x 15,000 bph.
"The plant is expected to be one of the most technologically advanced poultry-processing plants in the world, incorporating leading-edge food safety, environmental, and animal welfare processes and technologies. Construction at the London site is expected to begin in the spring of 2019, with start-up planned for the second quarter of 2021,” says CEO of Maple Leaf Foods, Michael McCain.
The NIRAS team lead by PM Johannes Pedersen has been a pleasure to work with - always extremely professional and the NIRAS insights have been very important part of designing this state of the art poultry plant.
Lou Cappa, VP Operations, Maple Leaf Foods
The Maple Leaf Foods Poultry Team is highly experienced in detailed planning and engineering for their existing factories. But considering the task at hand, the team decided a second set of eyes was needed to minimize risk and secure optimal design.
NIRAS was chosen to facilitate the Master Planning and Design to Tender phase as Subject Matter Expert and Project Facilitator to drive discussion and decisions forward without bias.
To validate the design and support the decision process the team developed a digital model of the production and used this to test future production weeks and break-down scenarios.
Maple Leaf’s VP Operations, Lou Cappa, gives the following verdict on NIRAS’ involvement in the process.
“The workshop approach developed and facilitated by NIRAS secures a high degree of confidence that the optimal solution has been chosen. Experience from other factory planning in other industries pork and beef processing with regards to overall factory layout has been integrated by an extensive number of factory visits in Europe as part of the planning.”
Mr. Cappa explains that design validation for the full installation has been carried out using NIRAS’ dynamic modelling. This approach has allowed the operations management to secure the plant functionality to meet production forecasts for specific production weeks at start of production and future operation.
“This project has been a true collaboration effort and will continue as such. There is a level of trust that has been built up over time and will only improve both business and the project overall. I could not have imagined a better team. The NIRAS team lead by PM Johannes Pedersen has been a pleasure to work with - always extremely professional and the NIRAS insights have been very important part of designing this state of the art poultry plant,” says Lou Cappa.
NIRAS has from 2015 supported the Maple Leaf Foods team in developing the project including the following activities:
• Validation of existing plans followed by prioritization of focus areas
• Layout workshops with all main suppliers
• Flow analyses regarding products, packing goods, waste, personnel and hygiene.
• Overview of main production lines.
• Main disposition of buildings and site.
• Overall implementation plan.
• Conceptual Design for Refrigeration and Process Ventilation, including input regarding optimal strategy for energy consumption.
• Considerations regarding use of by-products.
• Simulation model of slaughter, process and packaging area including design verification and simulation of largest/most complex production weeks for fully extended factory.
• Cost estimate (CAPEX).
• Consumption need for water, heat and electricity.
• Tender Documents (technical part) for reception area, slaughter, cut-up and de-boning
• Technical Evaluation of Suppliers proposal and support during tendering
NIRAS Food & Beverage Newsletter
Sign up to learn how our clients optimise production and drive sustainable progress.