How we work with water reduction in the pharmaceutical industry – A talk with process specialist, Justin Borrison
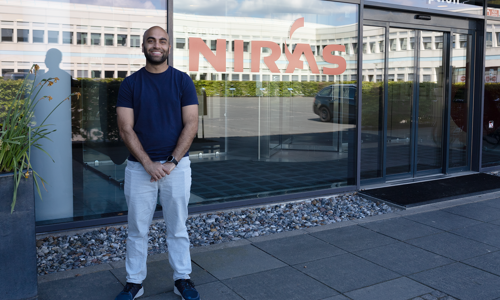
At NIRAS, our specialists work with global pharmaceutical manufacturers to rethink water processes, explore new ways of reusing water, and push the limits in terms of how to build sustainable production processes.
Across the life science sector, finding new ways to optimize and reduce water usage is becoming increasingly important. As the demand for pharmaceutical products is on the rise and more and more products are being developed and brought to market, climate change is altering the way companies can access water reserves, which brings with it a need for rethinking how water is used and reused throughout the various steps in the production processes.
We’ve caught up with our colleague and water and life science process engineer, Justin Borrison, who recently worked on a project to reduce water consumption by up to 44% at a major international pharmaceutical manufacturer.
Justin – a short introduction
Justin Borrison is an American process engineer whose work and sense of adventure has taken him around the world working for companies across the life science sector. He specializes in membranes with biological properties for water purification and holds an international Master’s degree in environmental/chemical engineering.
This was my first job when I joined NIRAS in 2023. I had been working for a previous company which manufactured filtration solutions and during my hiring process, NIRAS mentioned they had an interesting project with water savings and if I would be interested. So, when I started, the team explained the project and what would be required and I found it fascinating, innovative and requiring a lot of data analysis. This was different from what I had previously done, but that was the fun part since it was really challenging. Since it revolved around water it made the project a bit more interesting.
This project fascinated me due to its complexity. Most facilities try to collect water and then re-use it for non-critical purposes. However, this project was unique because we aimed to clean and reuse the water within the facility. The pharmaceutical industry uses chemicals and creates resistance drugs which are meant to evade/destroy certain compounds in the body - we wanted to use some of the cleaned water to be re-used with the drinking water entering the facility.
We also planned on identifying multiple parts of their facility so we could maximize their water savings. So, coming up with a method which can safely remove all these compounds was the unique part. We had to prove we could meet a high standard while trying to conserve as much water as possible. This was unique because this isn’t common practice within the industry and since it is novel for the pharmaceutical industry, this could lead to other industries following suit. The ability to adhere to drinking water standards is critical for these projects in the future.
This kind of work is becoming more and more common. As droughts and floods become more unpredictable, it affects how industry can approach water. It cannot be assumed that the same water supply will be there, so for industry to be resilient in the future, their processes must become more robust. We can see the trend throughout all industries as they try and reduce their water consumption while keeping up with demand.
Space, complexity, and robustness were a huge thing. Much of the space on site had been filled for production, so trying to squeeze in our facility was not easy. We needed to be clever with the placement, so it made sense (piping, flow, etc.) but at the same time it needed to fit/ be operable. This could involve multiple scaffolding or even trying to find the smallest crevice of space.
Since this was to be an add-on to the existing facility, it needed to be simple enough so that the operations didn’t affect current production. It should run in the background, with minimal interference, so a simple solution was preferred. At the same time, the system needed to be robust. It should provide water, but if there are any quality issues, it is discarded without interfering with production. The cleaned water generated needs to be added to the system but if it cannot supply enough water, there are other water sources which can take over. We don’t want our system to inhibit production in any manner.
Since this is was novel project, developing a correct methodology was critical. Figuring out the constraints and specifications has been a huge part. Working with different vendors helped us get insight into what is critical and getting the right people on the customer side is critical. While each customer is unique, it has helped set up the baseline so we can answer some of the customers' questions quicker. We also understand how the scope of the project can be expanded and customized.
I believe this is just the beginning. There was a plethora of options to save water and as you do something more and more times you can get better and be more ambitious. It would be cool if one day, we could save 90% of all water on site, and I don’t think we are that far off. After we dug deep into the data, there was potential to optimize the process, production, or even capturing water from different sources. These all need to be considered for both cost, size, feasibility, etc., but the potential is there!
This for sure can be used elsewhere, such as food and beverage, power-to-x, chemicals, etc. Every industry does a CIP so if it can be done in pharmaceuticals, then it can be done in other industries. I believe the payback is there and if industries want to become more sustainable, this is an easy first step.
Some of the cool technology discovered was:
As we got further into the process, more and more cool technologies popped up.
It is a lot of fun, as cliché as it might sound. One cool part was that NIRAS has done similar things before (Carlsberg water reuse project) but it was great that we had some guidance for this project. The people are passionate about sustainable solutions, so it was easy to ask for ideas and get inspiration. We were given guidelines and had backup from our management, but from there, we had a lot of freedom to apply our specialist knowledge.
The sparring of ideas is how you get a better design, and NIRAS has a great group of individuals from different fields who can help with this project. This aspiration makes working on projects so much better. Our attitude towards projects is always to find the best solutions, and you are always trying to innovate and come up with an even better solution.
If you want to read the story about the water reduction project mentioned above, go to: https://www.niras.com/projects/cutting-down-water-consumption-in-the-pharmaceutical-industry/