Insight
The future of aseptic manufacturing: Pioneering patient-centric solutions
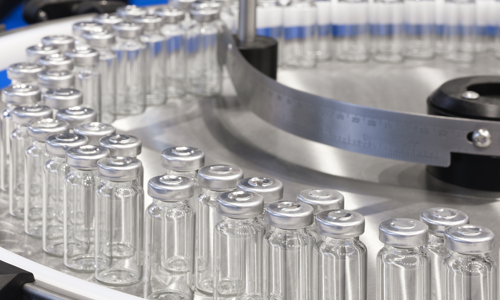
Credit: Matveev_Aleksandr
Insight
Credit: Matveev_Aleksandr
Aseptic manufacturing - commonly referred to as Fill Finish - serves as the backbone of safe, sterile drug production in the highly regulated pharmaceutical industry. From vaccines to biologics and other injectable medications, this critical process minimises microbial contamination while adhering to stringent current Good Manufacturing Practices (cGMP). The result is reliable products that enhance both patient safety and ease of administration.
As the pharmaceutical landscape evolves, the equipment and processes supporting drug production needs to as well. Recent years have witnessed a growing preference for single-dose single-use components, a trend that appeals to Contract Development and Manufacturing Organisations (CDMOs), biotech firms, and pharmaceutical companies alike.
Single dose single-use technologies bring a host of benefits:
Cost efficiency: Reduced need for cleaning, sterilisation, and downtime
Risk mitigation: Lower chances of cross-contamination between production batches
Ease of use: Streamlined production processes that adapt to diverse product requirements.
Meanwhile, Fill Finish lines are transitioning from traditional vial presentations to prefilled syringes (PFS) and cartridge-based systems.
The COVID-19 pandemic underscored the importance of scalable, efficient manufacturing solutions. Vial presentations became the format of choice due to their capacity to hold multiple doses, enabling faster production to meet global demand. However, as the healthcare landscape shifts towards more patient-centric care, the industry is now focusing on innovations that prioritise convenience, safety, and accuracy.
The increasing popularity of self-administered injectable drugs has paved the way for prefilled syringes (PFS). These solutions offer clear advantages for both patients and manufacturers:
For patients:
For manufacturers:
PFS technology embodies the shift towards patient-centric care, aligning with broader industry goals of improving health outcomes while optimising production efficiency.
To fully realise the potential of prefilled syringes, the pharmaceutical sector must address a critical challenge: Equipment adaptability. Modern filling lines need to accommodate interchangeable parts, enabling a seamless transition between vials, syringes, and cartridge-based systems. This flexibility is essential for CDMOs and in-house manufacturing teams striving to remain competitive in an ever-evolving market. With the rise of new product types manufacturing of aseptic and sterile products will require evolving technologies that accommodate various container and closure levels. Aseptic machinery has grown more complex to support various solutions. Most filling lines are now capable of filling vials, syringes, and cartridges interchangeably.
Most manual operations are being replaced with automated solutions that are compatible with single-use technology to comply with ANEX1 and other such guidelines. Transfers between process steps are being executed by robots to maintain aseptic environment without the need of human intervention. Much like visual inspection has become fully automated, we can expect other processes to become hyper automated as well.
To fully realise the potential of prefilled syringes, the pharmaceutical sector must address a critical challenge: Equipment adaptability. Modern filling lines need to accommodate interchangeable parts, enabling a seamless transition between vials, syringes, and cartridge-based systems.
The Fill Finish process is more than just a manufacturing step—it’s a commitment to delivering safe, effective, and accessible medications. With innovations like single-use components and prefilled syringes, the pharmaceutical industry is setting new standards in patient safety and operational efficiency.
…
As companies continue to adapt their processes and equipment, the future of aseptic manufacturing holds immense potential for ground-breaking advancements in global healthcare delivery. With the rise of single-use components and primary packaging, the industry will continue to face critique regarding company initiatives in place for promoting circular packaging. Such initiatives will allow for the reduction of the long-term environmental effects inflicted by the pharmaceutical industry. Reverse logistics chain scenarios have been popular and proven viable by more and more companies.