Insight
How does the plant-based sector compare to the meat industry in relation to by-products?
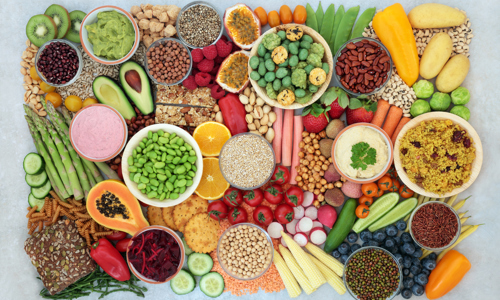
Insight
As demand for protein continues to shift towards plant-based, does the sector have lessons to learn from meat manufacturers? Below we discuss how the plant-based sector can take key learnings from the traditional meat industry and maximise the value of its by-products.
According to sustainability NGO WRAP, food surplus and waste in the UK is estimated to account for 7.2% of all food harvested, a total of 3.6 million tonnes, each year.
Although around 2 million tonnes of this surplus food is redistributed to animal feed or bio-based materials, 1.6 million tonnes per year are wasted. Much of this waste is from horticultural crops (54%) and cereals (30%), with just 8% of waste coming from livestock.
Traditional meat supply chains have spent decades refining their approach to the so-called ‘fifth quarter’, by optimising the output of each animal and extracting the highest possible value from its by-products.
Despite a growing shift in consumption for plant-based protein, the plant-based manufacturing sector is still some way behind its traditional meat counterparts when it comes to by-product valorisation.
The first practical step for plant-based protein brands and manufacturers is to develop a strong knowledge of the whole supply chain from field to fork. Only by understanding where waste streams are, can you begin to develop a strategy to drive value from it.
Developing more sustainable agricultural practices will be vital for planet health. A report from WWF found that 1.2 billion tonnes of food produced globally is lost before it even leaves the farm.
Precision agriculture, which uses satellite data, remote sensing devices, and data gathering technology to enable information-based farm management, is one example which could optimise overall output from the sector.
Manufacturers could also benefit from the increased efficiencies as a result from more widespread adoption of precision agriculture.
With better visibility of outputs from suppliers, manufacturing plants will be able to prepare and adapt their processes for precise quantities of raw materials, helping to minimise waste across the wider supply chain.
Once manufacturers have visibility of their waste streams, they can start to review their sustainability, assessing which waste products could be eliminated altogether, reduced, or reused.
When it comes to the manufacturing sector, plant-based is in a disadvantaged position compared to the traditional meat sector. The reason is that complicated manufacturing processes sometimes mean that it is easier to throw waste products away, rather than finding another use elsewhere in the supply chain.
However, as major players in the plant-based sector continue their maturity curves and margins are squeezed, putting the right materials and processes in place to minimise waste will be increasingly important.
This has been a relative weakness of the plant-based manufacturing sector, but putting process controls in place can have a huge role in optimising the output of products, increase operational efficiency and, perhaps most importantly, reduce waste.
Although the by-products market for traditional meat products is global, a more localised approach focused on symbiotic relationships between manufacturers could deliver even greater benefits for the plant-based protein sector.
As the strategic players in the market look to achieve greater efficiencies and increase margins, site selection will be an important consideration.
When choosing a site for a manufacturing plant, considering your by-products in a more strategic way, alongside more conventional requirements such as labour or energy, could see more complimentary plants co-locating to achieve mutual efficiencies.
One example of this pioneering industrial symbiosis is located in Kalundborg, Denmark, and uses a circular approach to production which turn a waste stream from one company into a resource for another.
Since 1972, the partnership has developed the world’s first industrial symbiosis with a circular approach to production. Kalundborg Symbiosis (http://www.symbiosis.dk/en/) includes more than 30 exchanges of materials, such as steam, gas, fly ash, gypsum, water and fertiliser, between more than 13 partners saving money and minimising waste.
This project was founded by the local municipality and the UK is much less advanced than Denmark in its approach to this type of project, so the UK will need investment and stimulus from the government to progress.
While plant-based protein supply chains remain relatively small and fragmented, if we can achieve a greater proportion of coordinated and collocated businesses, there is a huge opportunity for small, high growth manufacturers to achieve much greater value for their waste streams which could have a highly beneficial impact on both planet health and the growth of the plant-based sector.