Insight
Drying process is crucial in medical cannabis production
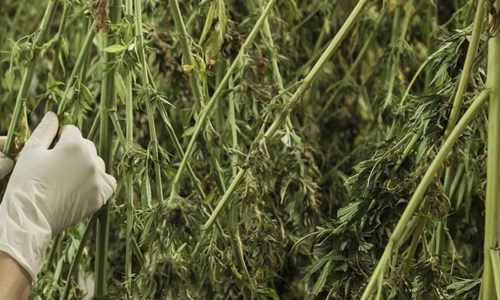
The drying process is key to ensure that the cannabis plants comply with medical regulatory requirements.
Insight
The drying process is key to ensure that the cannabis plants comply with medical regulatory requirements.
The drying process is essential in the production of medical cannabis in order to ensure clean products that meet the requirements set out by the Danish Medicines Agency and other health authorities. NIRAS's ventilation and GMP (Good Manufacturing Practice) engineers are experts in designing cannabis production facilities.
With a predicted turnover of 60 billion USD worldwide by 2025, medical cannabis is an industry in rapid growth. However, the production of medical cannabis is far from uncomplicated, and specialist knowledge is required to ensure that both production facilities and final products meet official requirements
The drying process is key to ensure that the plants comply with medical regulatory requirements. Improper drying may cause mold, in which case the product is no longer apt for medicinal use, and consequently the product must be discarded.
Focusing on three main issues will ensure stable and safe drying of cannabis after harvest:
The quality of the final product largely depends on how fast the water content is reduced and how it is controlled.
We find that some processes are automated as much as possible, by controlling the drying by the humidity and thereby running a standardized cycle.
Other methods include analysing the water content in the product, which helps to define the drying process.
In order to ensure controlled drying without external influences, it is important to set the right requirements for the facility and the process.
In our experience, CNC (Controlled, Not Classified) is sufficient in most cases. This allows sufficient control over the area to keep unwanted particles away from the product.
Outward air flow is ensured by maintaining greater room pressure in the drying room than in adjacent rooms. In addition, adequate filtration of air is established in ventilation units. These ensures a limited supply of unwanted particles from the outside in the fresh air supply.
In addition, the filtration prevents possible problems with mold, since the drying process often takes place by condensing moisture on a cooling surface, from which mold can arise. Incorporating routine replacement of filters avoids organic growth in the filter itself.
Even drying of products is an important factor, and therefore efficient air distribution is essential. It requires both a high air change in the room, as well as proper air supply and extraction principles.
NIRAS has helped to develop a room design that ensures an air flow parallel to the product, which often is placed on horizontal steel trays perforated at the bottom.
Even drying of the product is achieved via low and uniform air velocities through the trays, which in turn requires an air change of more than 30-60 times per hour.
Drying process as well as cleanliness requirements may vary greatly depending on the final product, e.g. leaves for inhalation (steam), further processing for oil or something else.
In NIRAS, ventilation and GMP specialists work closely together to design production facilities for drying cannabis. Services offered by our experts include:
Read more here.